BALANCE for TRADING NETWORKS – equipment scheduling and energy accounting
BALANCE allows you to significantly optimize the costs of retail chains and stores:
* Suspension of sales and failure of commercial equipment (due to power outages);
* Damage to products in refrigeration / freezers (untimely identification by staff of irregularities in the operation of refrigeration equipment in the store or in the process of delivery in the refrigerator);
* Damage to products in the warehouse (non-compliance of personnel with the requirements of temperature and humidity conditions in warehouses);
* Increased power consumption in the summer (air conditioning of the sales area).
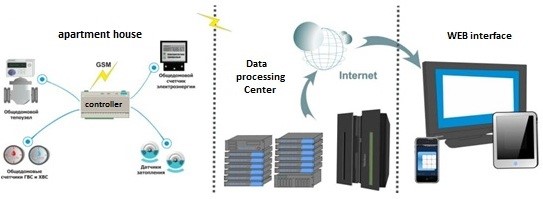
At the facility, metering devices and sensors are connected by the Customer, for this purpose, NO SPECIAL KNOWLEDGE IS NEEDED. According to the set schedule, the radio modules / controller / hub collects data and via the Internet (GSM / GPRS), transmits them to the BALANCE server. The sensor signals of the output parameters for the permissible limits are transmitted immediately.
In addition to electricity metering devices, metering equipment for heat energy, hot and cold water, temperature control sensors, as well as light sensors, can be connected to the BALANCE system. The BALANCE system can be installed on the Customer’s servers or work as a cloud solution, allowing you to receive all data via the Web interface using the Supplier’s server.
The functional BALANCE allows:
Immediately receive notifications from the BALANCE to the responsible employees of the trade network / store about critical deviations in the operation of the commercial refrigeration and freezing equipment of stores and refrigerated trucks, temperature conditions in the sales rooms and warehouses, and critical power outages. As well as other pre-emergency situations (pipe breakthrough, waterlogging, peak pressure, smoke, opening of office premises).
Receive a comparative report on the shops (by periods and among themselves), to identify the places of energy losses or the sluggishness of the administrators and sellers of the store.
To reduce internal energy losses, to prevent excessive conditioning and cooling of the sales areas, thereby significantly reducing the cost of electricity consumption. And vice versa, to ensure the comfort of customers’ stay in stores, strictly controlling the temperature in a given range set by the manager (not lower and not higher; the store employees themselves often set the cooling parameters of the trading rooms according to their subjective feelings).
Organize commercial accounting, recalculate energy resources, facilitate the work of the head of the AHO: to collect evidence and monitor all metering devices remotely; automatically generate a monthly report on energy consumption for submission to resource supplying organizations.
Origin of equipment and European certificate
When implementing projects, it uses its own equipment manufactured in Moldova: controllers, modems, converters, various control sensors, its own certified BALANCE software platform. For data transmission, the most effective technologies are used: DMesh and GSM data broadcasts. Pulse data acquisition interfaces from metering devices and “dry contact” or “open collector” sensors are supported. This allows you to achieve price leadership in the implementation and operation of the accounting system BALANCE.
All work on the installation of switching equipment, laying of connecting lines, connecting general home metering devices, can be performed by the CUSTOMER INDEPENDENTLY. The certification of the accounting system BALANCE was carried out at the Moldavian Center for Standardization and Metrology, which received European and global accreditation from the beginning of 2018.
An example of the calculation of efficiency: how much you can NOT LOSE
Major savings (on the example of a separate store) |
Average savings % | Current cost store euro / year | Expected savings euro / year |
Cost reduction due to food spoilage | 30 | 120 000 | 36 000 |
Heat loss (ventilation) | 10 | 90 000 | 9 000 |
Heat loss (overheating) | 10 | 90 000 | 9 000 |
Heat loss (thermal insulation) | 10 | 90 000 | 9 000 |
Electricity loss | 10 | 60 000 | 6 000 |
TOTAL ECONOMY PER YEAR: | 69 000 |
Set for yourself, make for others.
The BALANCE system is focused on technology transfer and deployment of screwdriver production to tens of thousands and millions of devices over the course of half a year. If your sales volume reaches 15,000 radio modules per year and MORE, it makes sense to deploy a screwdriver in the region, i.e. production of products according to proven technology, according to the documentation of the manufacturer with the provision of all necessary technological and test programs and equipment.
On the one hand, this is a more PROFITABLE option, since only a fixed payment for the transfer, training and support of the developed technology is made from the product. On the other hand, it is an opportunity to sell in your region and in the EU countries, the product PRODUCED in the EU. And these are WORK PLACES and TAXES coming to the LOCAL BUDGET.